[Quality Assurance Guide] Ensuring Product Quality When Importing from China
Product quality from China made easy! Learn how sourcing agents ensure top-notch standards with audits, inspections, and compliance checks.
12/9/20248 min read
![[Quality Assurance Guide] Ensuring Product Quality When Importing from China](https://assets.zyrosite.com/cdn-cgi/image/format=auto,w=812,h=344,fit=crop/YNqro9jB1VIg6bzd/124909-AQEyrlKJ6EtzNe8E.webp)
![[Quality Assurance Guide] Ensuring Product Quality When Importing from China](https://assets.zyrosite.com/cdn-cgi/image/format=auto,w=328,h=320,fit=crop/YNqro9jB1VIg6bzd/124909-AQEyrlKJ6EtzNe8E.webp)
When importing products from China, ensuring quality is critical to safeguarding your business reputation, satisfying customers, and avoiding costly returns or losses. Quality assurance (QA) is more than just a checkpoint; it’s a comprehensive strategy encompassing supplier evaluations, product inspections, compliance checks, and more.
China is known as the "world's factory," offering competitive pricing and a vast variety of goods. However, managing the consistency of those goods across borders can be challenging without proper oversight. This is where implementing a robust QA process comes into play.
This guide will equip you with essential insights and actionable strategies to maintain high standards when importing from China. Whether you're a first-time importer or a seasoned business owner, understanding how to mitigate risks and ensure product quality is invaluable.
Table of Contents
What is Quality Assurance, and Why is It Important?
How to Assess a Supplier’s Quality Control Processes
Types of Product Inspections
Implementing a Quality Control Plan
Common Quality Issues When Importing from China
Ensuring Compliance with International Standards
The Role of Sourcing Agents in Quality Assurance
Handling Defective Products
Leveraging Technology for Quality Assurance
What is Quality Assurance, and Why is It Important?
Definition of Quality Assurance
Quality assurance (QA) refers to the systematic processes put in place to ensure that products meet predefined standards before reaching customers. This includes verifying materials, inspecting production stages, and assessing final products.
Importance of Quality Assurance in Global Trade
With globalization, businesses often face challenges related to cultural differences, varying production standards, and lack of direct oversight. A robust QA system acts as a bridge, ensuring that products meet expectations regardless of where they are manufactured.
For example, 58% of global businesses reported supply chain disruptions related to quality issues in 2023, underlining the importance of preventive measures like QA.
Consequences of Poor Quality Products
Failing to implement effective QA can lead to:
Customer dissatisfaction: Damaged or subpar goods can tarnish your brand’s reputation.
Increased costs: Replacing defective products or compensating customers can drain resources.
Regulatory risks: Non-compliant products may face customs rejections or legal repercussions.
How to Assess a Supplier’s Quality Control Processes
Key Indicators of Effective Quality Control
A trustworthy supplier will have a well-documented quality control process. Key indicators include:
Clearly outlined inspection procedures.
Certifications like ISO 9001 or industry-specific accreditations.
A track record of delivering consistent product quality.
Questions to Ask Potential Suppliers
When evaluating a supplier, consider asking:
What quality control measures do you have in place?
How do you handle defects or deviations during production?
Can you provide references from other clients?
Building strong communication is vital for transparency and trust in the sourcing process.
Importance of Supplier Certifications
Certifications act as evidence of adherence to quality standards. For instance:
ISO 9001: International standard for quality management systems.
CE Marking: Compliance with European health, safety, and environmental protection standards.
Types of Product Inspections
Pre-Production Inspections
This step focuses on raw materials and components before production begins. Ensuring that inputs meet quality standards helps prevent issues further down the line.
During Production Inspections
Also known as in-line inspections, this process evaluates products at various stages of production. It allows you to:
Identify defects early.
Confirm adherence to design specifications.
Pre-Shipment Inspections
A critical final step, pre-shipment inspections verify that the finished products meet your quality criteria. This includes:
Checking for defects.
Verifying packaging standards.
Ensuring correct labeling and documentation.
Implementing a Quality Control Plan
A solid quality control (QC) plan is essential for ensuring product consistency and minimizing risks during the import process. While quality assurance focuses on setting standards, quality control emphasizes verifying that these standards are met.
Steps to Create a Quality Control Plan
Define Quality Standards:
Identify the specific requirements your product must meet. This includes material quality, functionality, appearance, and packaging. For instance, if you're importing electronics, define metrics like durability, compliance with certifications, and user safety.Document Procedures:
Create a clear, written plan outlining how inspections will be conducted. Include details such as:Inspection frequency.
Tools or technology required.
Reporting and documentation methods.
Set Up Communication Protocols:
Ensure seamless communication between your team, suppliers, and quality inspectors. Sharing real-time updates can help address issues quickly.Regular Training:
If you’re directly involved in inspections, train your team to recognize quality deviations. Alternatively, rely on experienced sourcing agents like Smart Win to handle inspections professionally.
Setting Quality Standards and Metrics
Quality standards should be specific, measurable, and relevant to your product category. For example:
Tolerance levels: Acceptable variation limits in dimensions or weights.
Functionality tests: Ensuring the product performs as intended.
Durability checks: Verifying the product's longevity under normal use.
Having predefined metrics makes it easier to evaluate suppliers and products objectively.
Training Staff on Quality Control Procedures
Well-trained staff or partners can make a significant difference in maintaining product quality. Key training areas include:
Recognizing common defects.
Using inspection tools effectively.
Preparing thorough reports on inspection findings.
Alternatively, a sourcing agent can provide specialized knowledge and manage this process for you.
Common Quality Issues When Importing from China
Understanding potential quality challenges can help you proactively address them.
Types of Defects to Watch For
Defects are generally categorized into three types:
Critical defects: These pose safety risks or make the product unusable.
Major defects: Significant deviations that might affect customer satisfaction but not safety.
Minor defects: Small issues that don’t affect the product’s core functionality.
Understanding Defect Rates and Their Impact
Defect rates, often expressed as "acceptable quality limits" (AQL), define how many defects are permissible in a batch. For example:
An AQL of 1% for critical defects ensures no more than 1 defective item per 100 is accepted.
Monitoring AQL during inspections helps balance quality expectations and production realities.
Case Studies of Common Issues
Electronics: Overheating or non-compliance with safety standards.
Textiles: Incorrect sizing or inconsistent stitching.
Toys: Use of harmful materials like lead-based paint.
To avoid such problems, it’s crucial to conduct pre-shipment inspections or hire a sourcing agent who can address these issues early.
Ensuring Compliance with International Standards
International compliance is not just a legal requirement; it’s also a quality benchmark that instills confidence in your customers.
Overview of Relevant Compliance Standards
RoHS (Restriction of Hazardous Substances): Ensures electronic products are free from certain hazardous materials.
FDA Approval: Required for food, cosmetics, or medical imports into the U.S.
ISO Standards: Cover various product categories, ensuring globally recognized quality benchmarks.
Importance of Testing and Certification
Certified products build trust in the marketplace. Before shipping, ensure that your goods undergo third-party testing where applicable. Examples include:
Chemical testing for cosmetics or toys.
Durability testing for furniture.
Working with Third-Party Testing Labs
Third-party testing provides an unbiased evaluation of product quality and compliance. Some benefits include:
Ensuring adherence to national and international regulations.
Protecting your brand from recalls or penalties.
Using a sourcing agent allows you to leverage established partnerships with reliable testing labs, saving you time and ensuring thorough evaluations.
The Role of Sourcing Agents in Quality Assurance
Sourcing agents play a pivotal role in ensuring quality control when importing from China. Their on-the-ground expertise, established relationships with suppliers, and systematic processes make them invaluable partners for maintaining product quality.
Benefits of Using a Sourcing Agent for Quality Control
Local Market Knowledge:
Sourcing agents are well-versed in the nuances of the Chinese manufacturing landscape. They know which suppliers are reliable and how to navigate challenges like communication barriers and cultural differences.Comprehensive Inspections:
From conducting factory audits to pre-shipment inspections, sourcing agents ensure every stage of production aligns with your quality standards.Risk Mitigation:
By identifying potential issues early, sourcing agents help avoid costly errors, such as defective products or shipping delays.
How Sourcing Agents Conduct Supplier Audits
Supplier audits are critical for verifying a factory’s capabilities and adherence to quality standards. A professional sourcing agent typically evaluates:
Factory certifications: Check validity of business license, ensuring compliance with ISO, CE, or other industry standards.
Production capacity: Verifying whether the supplier can meet your order requirements.
Workplace conditions: Checking for ethical labor practices and safety measures.
Regular audits allow agents to establish long-term partnerships with trustworthy suppliers.
Communication Between Sourcing Agents and Suppliers
Sourcing agents act as intermediaries, ensuring your quality expectations are clearly communicated to suppliers. This minimizes misunderstandings and ensures smoother operations. Their fluency in local languages and understanding of cultural norms enhance supplier relationships.
Managing Defective Products
Despite rigorous quality assurance efforts, defects can occasionally slip through. Having a clear strategy for managing defective products is essential to minimize losses.
Developing a Return Policy with Suppliers
A robust return policy should include:
Timeframes: Specify how long after delivery a return can be initiated.
Responsibility clauses: Determine who bears the cost of return shipping or rework.
Negotiate these terms with your supplier upfront to avoid disputes later.
Steps for Handling Defective Goods
Document the Issue:
Take photos and detailed notes on the defect. This evidence will support your case when discussing the issue with the supplier.Contact the Supplier Immediately:
Notify them about the defects and share the documentation.Negotiate Resolutions:
Options may include refunds, replacements, or discounts on future orders.
Sourcing agents can assist in these negotiations, ensuring a fair outcome.
Legal Considerations for Returns and Refunds
If disputes arise, ensure your contract includes legal recourse options. For instance, specify arbitration methods or governing laws that will apply in such cases.
Leveraging Technology for Quality Assurance
Modern technology offers numerous tools to enhance quality assurance, making it easier to track and manage processes remotely.
Tools for Monitoring Production Quality
Digital platforms can provide real-time updates on production stages, such as:
Cloud-based QC platforms: Centralize all quality control data for easy access.
IoT-enabled devices: Monitor manufacturing equipment performance to detect anomalies.
Software for Managing Supplier Relationships
Supplier management software helps streamline communication and track performance metrics. Benefits include:
Centralized documentation of contracts and inspection reports.
Alerts for upcoming audits or reorders.
Utilizing Data Analytics for Quality Improvement
Analyzing defect patterns or production delays over time can reveal actionable insights. For example:
Identifying recurring issues with a particular supplier.
Adjusting production schedules to minimize errors.
Conclusion
Recap of Key Insights
Maintaining product quality when importing from China requires meticulous planning, consistent monitoring, and clear communication. From supplier audits and product inspections to leveraging modern technology, every step of the process contributes to delivering goods that meet your expectations.
Partnering with an experienced sourcing agent like Smart Win simplifies this complex process. Their expertise in quality control, supplier audits, and compliance ensures that your imports not only meet but exceed industry standards.
Final Thoughts
Quality assurance is more than just a checklist; it’s a commitment to your customers and your brand. By following this guide and collaborating with trusted professionals, you can safeguard your business against quality issues and build a reputation for excellence in your industry.
Ready to elevate your importing game? Connect with Smart Win today to ensure your products meet the highest quality standards.
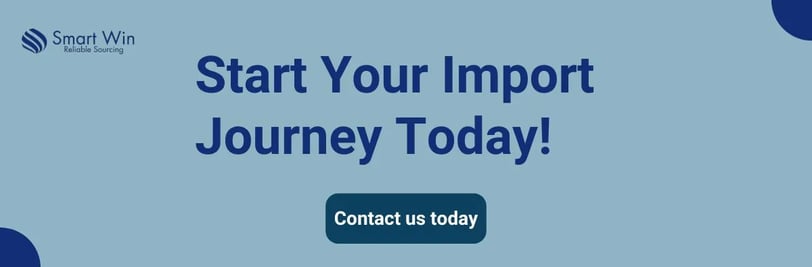
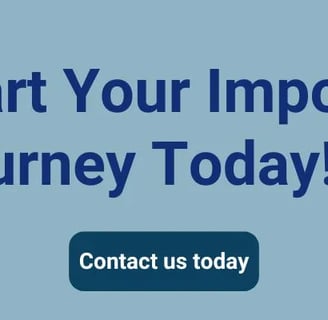
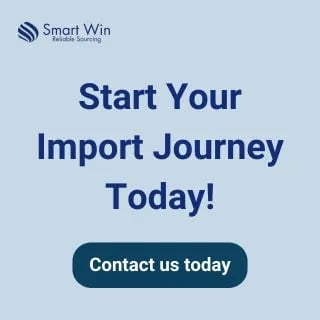
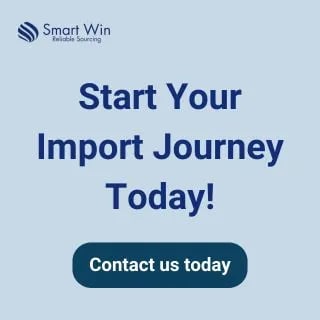
FAQs:
1. How can I verify the authenticity of supplier certifications in China?
To verify supplier certifications, you can check directly with the issuing bodies or use third-party verification services. Look for certifications like ISO or CE and confirm their validity through official registries. Sourcing agents can also assist in vetting these documents.
2. What is the difference between quality assurance and quality control?
Quality assurance focuses on preventing defects by establishing systematic processes and standards, while quality control involves inspecting products to identify and address defects. Both are crucial for maintaining high standards when importing.
3. How can I negotiate better quality standards with a supplier?
When negotiating, clearly outline your quality expectations in the contract, provide detailed product specifications, and request samples. Building a strong relationship with the supplier and using a sourcing agent can also improve negotiation outcomes.
Get in touch
Our Address
No.202 Huanshi West Rd, Yuexiu District Guangzhou, China
Contact Us
Working hours
Monday - Saturday
9:00 - 18:00
( Beijing Standard Time )
Smart Win Services
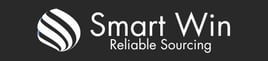
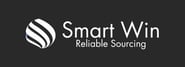
Company