The Importance of Quality Control in China Sourcing
The Importance of Quality Control in China Sourcing: Ensure product reliability, mitigate risks, and protect your brand with effective quality control processes
10/17/202410 min read
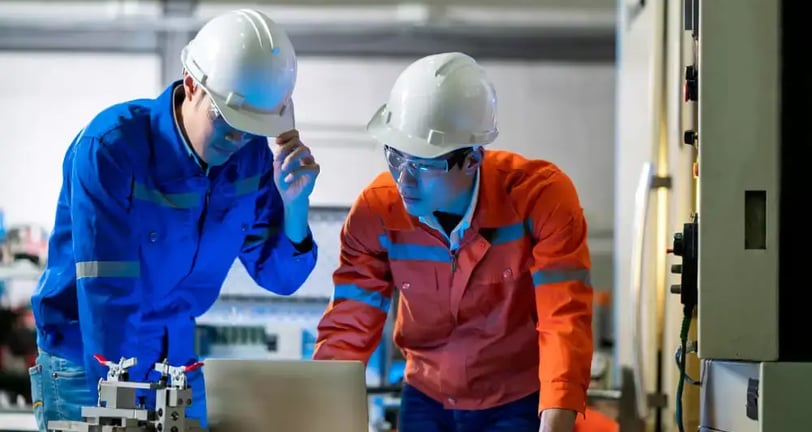
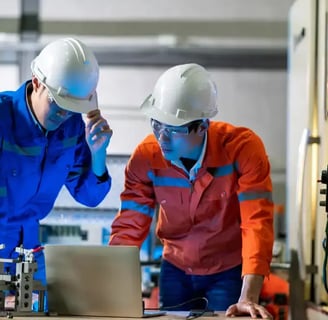
Introduction
When sourcing products from China, one of the most crucial aspects businesses need to focus on is quality control. With the growing number of global brands turning to China for affordable manufacturing, ensuring that the products meet specific quality standards has become essential. In 2024, quality control remains a top priority for businesses to protect their brand reputation, reduce risks, and ensure customer satisfaction. Effective quality control not only ensures that the products are compliant with industry standards, but it also helps in minimizing defects, improving reliability, and maintaining customer trust.
In this article, we’ll explore why quality control is vital when sourcing from China, what the key components of the process are, and how to establish clear quality expectations with suppliers.
Table of Content:
Why is Quality Control Essential When Sourcing from China?
Key Components of an Effective Quality Control Process
How to Establish Clear Quality Expectations with Suppliers
Types of Inspections You Should Conduct During the Sourcing Process
How Cultural Differences Impact Quality Control in China
How to Handle Defective Products Found During Inspections
The Role of Third-Party Quality Control Agencies
Common Challenges in Quality Control When Sourcing from China
How Technology Enhances Quality Control Processes
Conclusion: Strengthening Your China Sourcing Strategy with Quality Control
Smart Win: Your Reliable Sourcing Agent in China
Why is Quality Control Essential When Sourcing from China?
1. Risk Mitigation
When sourcing products from another country, there are inherent risks. Quality control helps mitigate those risks by ensuring that the products meet the required standards before they leave the factory. This process reduces the chances of defective products reaching the end customer, which could lead to returns, refunds, or even legal disputes.
2. Ensuring Compliance with Standards
Different markets have different regulations and compliance standards. Implementing thorough quality control ensures that the products you source from China comply with these regulations, whether it's safety standards, performance metrics, or certification requirements. This is especially critical for industries like electronics, toys, and medical equipment.
3. Protecting Brand Reputation
Your brand’s reputation is one of your most valuable assets. Poor quality products can severely damage your brand image, leading to negative reviews, loss of customers, and even a decline in revenue. With robust quality assurance processes in place, you can protect your brand by ensuring only the best products make it to market.
Key Components of an Effective Quality Control Process
1. Defining Quality Standards
The first step in any effective quality control process is clearly defining the quality standards that your products need to meet. These standards should be aligned with your target market’s expectations and regulatory requirements. Whether it's the durability of a product, its aesthetic finish, or its functionality, setting clear benchmarks is essential.
2. Supplier Audits and Inspections
To ensure that your supplier can meet your quality standards, conducting supplier audits is critical. This involves assessing the supplier's manufacturing processes, facilities, and workforce. Regular product inspections should also be conducted throughout the production process to catch any issues early on.
3. Continuous Monitoring and Feedback
Once the production begins, it’s crucial to maintain ongoing quality checks to ensure the products are being made according to the agreed-upon standards. Providing continuous feedback to your suppliers helps in addressing any issues early, reducing the chances of costly mistakes down the line.
How to Establish Clear Quality Expectations with Suppliers
Establishing clear quality expectations with your Chinese suppliers is essential for a smooth sourcing process. Miscommunication or vague requirements can lead to manufacturing errors, delays, or products that don't meet your standards. Here’s how you can avoid those pitfalls and set clear expectations for quality:
1. Importance of Detailed Specifications
When working with suppliers, the more detailed your product specifications are, the better. This includes everything from material types, dimensions, and weight to color, functionality, and packaging requirements. It’s crucial to provide all technical drawings, prototypes, or samples if possible. A lack of detailed information often leads to misunderstandings about the final product. By being specific upfront, you significantly reduce the chances of mistakes.
For instance, providing clear quality standards ensures suppliers know exactly what they need to meet. Without clear details, you may receive products that don’t match your vision or market requirements.
2. Effective Communication Strategies
One of the biggest challenges in China sourcing is the language and cultural barriers. To mitigate these, ensure all communication is straightforward and concise. Using visual aids, such as diagrams and videos, can help bridge language gaps and explain product specifications better than words alone.
Building a strong communication loop with suppliers is equally important. Using project management tools and regular check-ins can help keep both sides aligned. Moreover, always get everything in writing to avoid any misunderstandings. A written agreement outlining every expectation, delivery date, and quality standard serves as a point of reference and ensures accountability.
3. Utilizing Written Agreements
Written agreements or contracts that include clear terms and conditions are crucial for protecting your business. These should define the quality control processes, inspection schedules, and any penalties for not meeting the quality standards. Make sure that the agreement includes clauses covering product defects and the supplier’s responsibility for rectifying them, whether through a refund, replacement, or rework.
Having everything laid out in a formal agreement helps avoid disputes later in the process and ensures that everyone involved knows the expectations from the very beginning.
Types of Inspections You Should Conduct During the Sourcing Process
A strong quality control process includes several types of inspections at various stages of production. Conducting inspections early and often will help you catch potential issues before they snowball into larger problems.
1. Pre-Production Inspections
Before production starts, a pre-production inspection is carried out to verify that the supplier fully understands your requirements and that the materials they are using meet the agreed-upon standards. This step is critical to prevent issues later in the production process, such as using the wrong materials or incorrect product dimensions.
2. In-Process Inspections
During the manufacturing phase, in-process inspections are done to monitor the production and ensure that everything is going according to plan. These inspections can catch potential problems early, such as defects in workmanship, incorrect assembly, or poor quality materials. Addressing these issues in the middle of production is much easier (and cheaper) than finding them at the end of the process.
Regular in-process quality control ensures that your supplier maintains the expected standards throughout the production cycle, giving you peace of mind that your products are on track to meet your requirements.
3. Final Product Inspections
The last line of defense in quality control is the final product inspection. This occurs once the production is complete and before the goods are shipped. A thorough inspection at this stage can catch any defects that may have slipped through earlier checks. Everything from product appearance to functionality and packaging is evaluated. Any defects found at this stage can be addressed before the shipment leaves the supplier’s facility, avoiding the expensive and time-consuming process of returning goods after they’ve arrived in your country.
By carrying out comprehensive inspections throughout the production process, you ensure that the products you receive are of high quality and meet your expectations.
How Cultural Differences Impact Quality Control in China
1. Understanding Chinese Business Practices
Cultural differences can affect every aspect of doing business in China, including quality control. Understanding Chinese business practices and communication styles is essential to establishing a strong working relationship with suppliers. For instance, in China, it’s common to avoid directly pointing out flaws or disagreements, which can make it challenging to enforce quality standards if the issue is not handled carefully.
2. Navigating Communication Barriers
While many Chinese manufacturers have staff that speaks English, there can still be communication barriers that complicate the quality control process. Misinterpretations of your quality requirements can lead to mistakes. That’s why using third-party quality control agencies who understand both the language and the local business culture can be beneficial. They act as a bridge, ensuring that your quality expectations are communicated clearly and correctly to the supplier.
3. Building Trust with Suppliers
Building long-term, trusting relationships with your suppliers in China can significantly enhance the quality control process. When suppliers see you as a valuable and ongoing partner, they’re more likely to prioritize your needs and adhere to the agreed-upon standards. Visiting the factory in person, conducting regular quality checks, and maintaining open lines of communication can all help build that trust.
How to Handle Defective Products Found During Inspections
Even with the best quality control processes, defects can still arise during production. When sourcing from China, handling defective products effectively is crucial for maintaining your business's reputation and ensuring customer satisfaction. Here are some strategies for managing defective products:
1. Strategies for Addressing Defects
When defects are found during inspections, the first step is to determine the severity and extent of the issue. Minor defects can often be corrected without significant disruption, while major defects may require reworking or even halting production. Clear communication with your supplier is essential here. You should have a defect resolution plan outlined in your contract that details how issues will be handled.
In many cases, suppliers will offer to rework or replace the defective products, but you need to ensure this process doesn’t delay your overall timeline too much. Negotiating with your supplier about these corrections will help ensure the defects are resolved quickly and efficiently without compromising quality.
2. Negotiating Returns or Remakes
When significant defects occur, you may need to negotiate for a return or remake of the products. Having a strong written agreement in place that outlines these scenarios will make the negotiation process smoother. In some instances, suppliers may try to negotiate partial refunds or discounts on future orders rather than providing a full return or replacement. This can be a viable solution, depending on the severity of the issue and your business needs.
It’s also essential to document all instances of defects and your communication with the supplier to ensure accountability throughout the process.
3. Legal Considerations and Documentation
In some cases, you may need to involve legal professionals if disputes arise over defective products. This is where having a robust contract comes into play. Make sure you have clauses in your contract that clearly state the supplier’s responsibility in case of defective products, the steps for resolving disputes, and any legal recourse you can take if necessary.
Documentation is critical in these situations. Keep detailed records of all inspections, defects, and communications with your supplier. This will be invaluable if you need to escalate the situation or pursue legal action.
The Role of Third-Party Quality Control Agencies
Working with third-party quality control agencies can be a game-changer when sourcing from China. These agencies act as independent inspectors, ensuring that your products meet your quality standards without bias.
1. Benefits of Independent Inspections
Third-party agencies provide an objective and thorough evaluation of your products, often with a level of detail that may be challenging to achieve internally. They offer unbiased inspections at various stages of production, including pre-production, in-process, and final product inspections. Since these agencies have extensive experience working with international buyers, they understand the specific quality concerns you may have and can help bridge cultural and language gaps.
Moreover, using a third-party agency reduces the likelihood of disputes with suppliers, as both parties have agreed on a neutral entity to evaluate the products.
2. Choosing a Reputable QC Agency
Selecting a reputable quality control agency is critical. Look for agencies that have experience in your industry and a strong track record of helping businesses like yours. Check references and reviews from other clients to ensure they are reliable and thorough.
You should also confirm that the agency uses international quality standards and can provide detailed reports that include photos, test results, and recommendations for addressing any issues.
3. Cost Considerations
The cost of hiring a third-party quality control agency is an investment in the long-term success of your business. While there are fees associated with their services, these costs are often far outweighed by the savings gained from avoiding defective or non-compliant products. In many cases, the cost of reworking or replacing defective products can be significantly higher than the fees for regular inspections.
Common Challenges in Quality Control When Sourcing from China
While implementing a robust quality control process can reduce risks, there are still some challenges that businesses may face when sourcing from China.
1. Cultural Misunderstandings
As mentioned earlier, cultural differences can create misunderstandings between buyers and suppliers. For instance, Chinese suppliers may be reluctant to communicate problems during production, fearing it will damage the business relationship. This can lead to unresolved issues that affect the final product quality.
To address this, fostering open and honest communication with suppliers is essential. Building strong relationships where feedback is encouraged can help prevent misunderstandings and ensure a smoother production process.
2. Variability in Manufacturing Standards
Not all manufacturers in China operate at the same level of quality. There can be significant variability in manufacturing standards from one factory to another. That’s why it’s crucial to conduct supplier audits before committing to a partnership. An audit allows you to verify that the factory has the necessary processes and certifications to meet your quality expectations.
By working with reputable suppliers and conducting thorough pre-production inspections, you can minimize the risk of working with factories that do not meet your standards.
3. Logistical Issues
Even when the products meet your quality requirements, logistical issues can still arise. Delays in shipping, customs complications, and damaged goods during transit are all potential challenges that need to be managed.
Partnering with a sourcing agent or logistics expert who understands the intricacies of international trade can help you navigate these issues. Ensuring that proper packaging and handling procedures are followed during the production and shipping process is also essential to avoid damage.
How Technology Enhances Quality Control Processes
Advancements in technology are making quality control more efficient and effective, especially when sourcing from China.
1. Utilizing Software for Tracking and Reporting
Many businesses are now using specialized quality control software to track inspections, defects, and supplier performance. These tools allow you to monitor quality in real-time, generate reports, and identify patterns or recurring issues.
2. Automation in Inspection Processes
In some industries, automation is becoming a critical part of the inspection process. Automated systems can quickly scan and evaluate products for defects, ensuring a higher level of accuracy and consistency. While not yet applicable to every industry, automation can be particularly beneficial for high-volume production runs where human error might otherwise miss defects.
3. Data Analytics for Continuous Improvement
Leveraging data analytics is another way businesses are improving their quality control processes. By analyzing data from past inspections and product performance, companies can identify trends and areas for improvement. This data-driven approach enables continuous improvement and helps businesses stay ahead of potential quality issues.
Conclusion: Strengthening Your China Sourcing Strategy with Quality Control
In conclusion, quality control is a critical component of any successful China sourcing strategy. From setting clear expectations with suppliers to leveraging third-party inspections and utilizing technology, ensuring product quality protects your brand and bottom line. By investing in robust quality assurance measures, you can navigate the challenges of sourcing from China and consistently deliver high-quality products to your customers.
By incorporating the right strategies, building strong relationships with suppliers, and using tools like third-party agencies, businesses can mitigate risks and improve the overall success of their sourcing efforts.
Remember, quality control is not just about preventing defects—it's about creating a reliable and efficient sourcing process that builds long-term success.
Smart Win: Your Reliable Sourcing Agent in China
Smart Win is a highly reputable China sourcing agent. With 32 years of experience navigating the difficulties of the Chinese market, and exporting to 28 countries. Provides comprehensive services such as supplier sourcing, price negotiation, quality inspection, and shipping, resulting in a smooth sourcing experience. Smart Win focuses on securing high-quality products at competitive prices, as well as offering product customization services as needed. Smart Win charges their customers a commission fee of 2% to 5%, depending on the value of the order.
Get in touch
Our Address
No.202 Huanshi West Rd, Yuexiu District Guangzhou, China
Contact Us
Working hours
Monday - Saturday
9:00 - 18:00
( Beijing Standard Time )
Smart Win Services
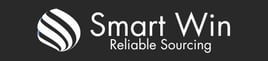
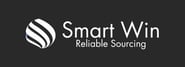
Company